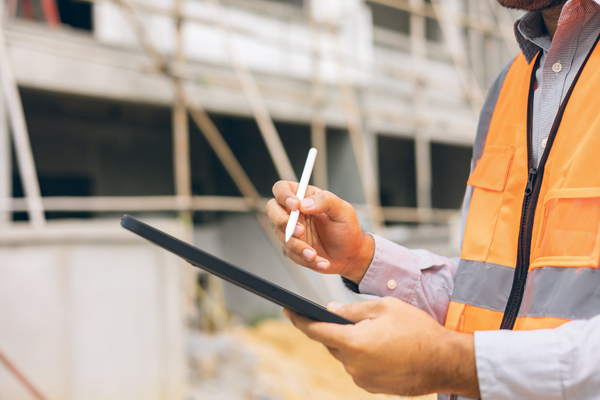
Laserrevolution in der Bauwerksintegritätsprüfung
Die Bauwerksinspektion wird durch laserbasierte Messsysteme revolutioniert, die eine schnelle, präzise und digitale Datenerfassung ermöglichen. Der Einsatz von Laserscannern zur Vermessung der Geometrie von Bauwerken und zur Erkennung von Oberflächenschäden ist bereits gängige Praxis. Zukünftig wird es jedoch auch möglich sein, mithilfe von Lasern verdeckte Schäden in der Tiefe aufzuspüren, was bisher nur mit dem Hammerschlagtest möglich war.
Die Herausforderung der Sichtprüfungen
Die visuelle Inspektion bleibt eine weit verbreitete Methode zur Beurteilung des Zustands von Bauwerken. Doch was passiert, wenn Schäden unter der Oberfläche auftreten? Versteckte Hohlräume oder Ablösungen des Materials, wie Delaminationen, können Anzeichen für bevorstehende größere Schäden sein. Sie frühzeitig zu erkennen, ist ein wesentlicher Bestandteil der vorausschauenden Instandhaltung von Infrastrukturbauwerken wie Tunneln, Brücken und Staumauern sowie für kritische Baumaßnahmen wie den Rückbau von Atomkraftwerken. Ein Forschungsteam am Fraunhofer IPM hat ein System entwickelt, das zerstörungsfreie Delaminationsprüfungen mithilfe eines gepulsten Lasers ermöglicht.
Quantifizierbare Messdaten für vorausschauende Instandhaltung
Der Hammerschlagtest war bislang das bevorzugte Mittel, um verborgene Fehlstellen wie Delaminationen aufzuspüren. Dabei wird die gesamte zu prüfende Oberfläche von Hand mit einem speziellen Prüfhammer abgeklopft, was bei großen Objekten zeitaufwändig ist. Als Sensor dient hierbei allein das menschliche Ohr, was subjektive Ergebnisse liefert und eine objektive Bewertung erschwert. Für zeitgemäßes Zustandsmonitoring und Building Information Modeling (BIM) sind digitale Messdaten erforderlich.
Das vom Fraunhofer IPM entwickelte berührungslose Verfahren verwendet einen starken gepulsten Laser, um den mechanischen Hammerschlag zu imitieren. Der Laser erzeugt einen Plasmablitz vor der Objektoberfläche, ohne diese zu beschädigen. Verbergen sich Delaminationen oder Defekte unter der Oberfläche, regt die plasmainduzierte Schockwelle charakteristische resonante Schwingungen der Oberfläche an, ähnlich wie beim Hammerschlag. Die Schwingungen werden mithilfe eines zweiten Lasers, einem Laser-Doppler-Vibrometer (LDV), erfasst. Dies ermöglicht eine genaue Bestimmung von Größe und Tiefe der Hohlräume und Defekte. Das System kann 100 m2 mit einem 10 cm-Messraster in nur 17 Minuten prüfen und lässt sich durch Optimierungen weiter beschleunigen.
Zuverlässige Messungen aus der Ferne möglich
Bei Vergleichsmessungen mit dem klassischen Hammerschlagtest aus zwei Metern Entfernung konnte das laserbasierte System Delaminationen mit einer Größe von wenigen Zentimetern sicher erkennen, die mit der mechanischen Methode übersehen wurden. Das Forschungsteam arbeitet nun daran, das System für den praktischen Einsatz zu optimieren und ein produktives System zu entwickeln.